Understanding the Role of Die Cast Mold Manufacturers in Modern Metal Fabrication
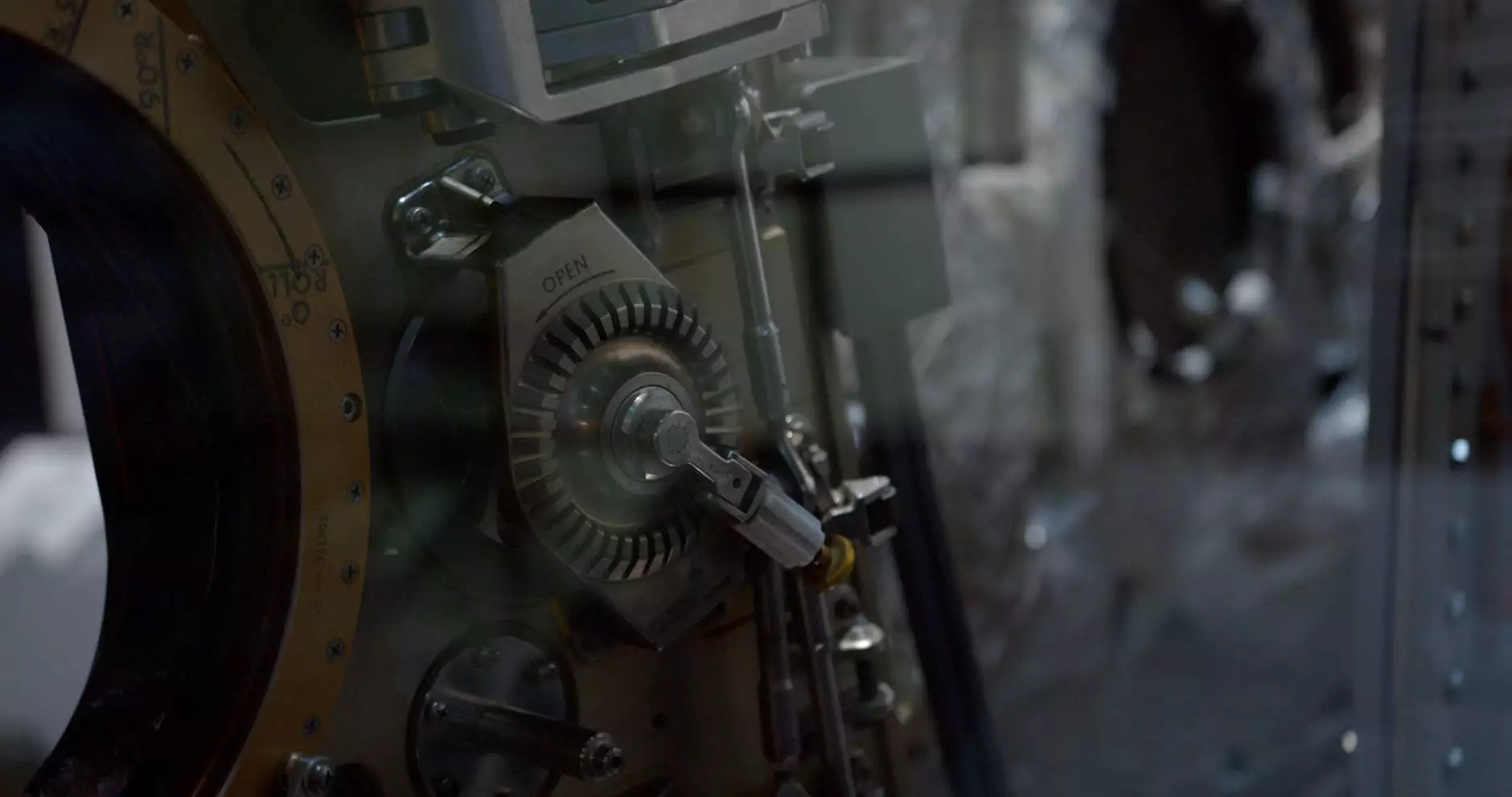
In the dynamic world of manufacturing, the significance of die cast mold manufacturers cannot be overstated. These specialized entities play a crucial role in the metal fabrication process by creating molds that allow for the efficient and precise production of complex metal parts. This article delves into the implications of die casting, the intricacies of mold manufacturing, and the broader impact these processes have on various industries.
The Importance of Die Casting in Metal Fabrication
Die casting is a metal casting process that utilizes molds, called dies, to produce parts through the injection of molten metal under high pressure. This technique is revered for its ability to create high-volume parts with exceptional detail and superior surface finishes. The key advantages of die casting include:
- Precision: Die casting allows for high dimensional accuracy and tight tolerances, making it ideal for components that require exact specifications.
- Complex Geometries: Manufacturers can produce intricate designs that would be difficult or impossible with other manufacturing methods.
- Reduced Waste: The die casting process minimizes material wastage due to its precise nature, contributing to lower production costs and an environmentally friendly approach.
- Rapid Production: The ability to produce large quantities of parts in a short time frame enhances productivity and meets market demands effectively.
Key Components of Die Casting
1. The Die
The die is a critical component of the die casting process. Typically made from steel or other durable materials, the die is designed to withstand the intense pressures involved in injection casting. It consists of two halves: the ejector side and the nozzle side. Here’s a breakdown:
- Ejector Side: Facilitates the removal of the cast part after solidification.
- Nozzle Side: Holds the molten metal during the injection process.
2. The Injection System
This system is responsible for delivering molten metal into the die. It includes the ladle and the high-pressure injection mechanism. The speed and pressure at which the metal is injected significantly affect the final product’s quality.
3. Temperature Control
Proper temperature management is essential in die casting. Maintaining the right temperature ensures that the metal flows smoothly into the mold and cools evenly, minimizing defects such as warping or uneven cooling.
Selection of Die Cast Mold Manufacturers
Choosing the right die cast mold manufacturers is vital to the success of any metal fabrication project. Potential clients should consider several factors when selecting a manufacturer, including:
1. Experience and Specialization
Manufacturers with a robust track record in specific industries often understand the unique requirements and challenges associated with those fields. For instance, automotive die cast manufacturers must be well-versed in producing parts that meet stringent safety and performance standards.
2. Quality Assurance
A commitment to quality is paramount. Reputable manufacturers often employ rigorous testing and quality control measures to ensure every part produced meets high standards. Certifications like ISO can be indicators of a manufacturer's dedication to maintaining quality.
3. Advanced Technology
The die casting industry continually evolves, with new technologies enhancing production efficiency and precision. Manufacturers that invest in advanced machinery and processes can often provide superior products and faster turnaround times.
4. Customer Support and Collaboration
A partner who understands your needs and collaborates effectively can make all the difference. Look for manufacturers willing to engage in consultation and adapt designs based on client feedback.
The Broader Impact of Die Casting in Industries
Die casting is a pervasive technique used in various industries, including:
1. Automotive Industry
The automotive sector relies heavily on die casting for creating components like engine blocks, transmission housings, and wheel rims. The combination of lightweight materials and strength enhances vehicle performance and fuel efficiency.
2. Aerospace
In aerospace, precision and weight reduction are critical. Die cast parts often serve in structural components and other applications where other manufacturing techniques may fall short due to weight constraints.
3. Electronics
Die cast manufacturers produce components for various electronic devices, ensuring adequate heat dissipation and protection in metal housings. The smooth surface finishes achieved enhance the aesthetic appeal and functionality of these products.
4. Consumer Products
Many everyday consumer products, such as kitchen appliances and tools, also benefit from die casting. The ability to produce intricate designs at a low cost allows for innovation and variety in the products available in the market.
Future Trends in Die Casting
As industries evolve, so does die casting. Some notable trends that die cast mold manufacturers like DeepMould.net are embracing include:
1. Automation and Robotics
The introduction of robotics into the die casting process boosts efficiency and minimizes human error. Automation enhances production capabilities and often leads to reduced costs in the long run.
2. Sustainable Practices
With the increasing focus on sustainability, die cast manufacturers are adopting eco-friendly practices. These include using recyclable materials and reducing energy consumption in the production process.
3. Advanced Materials
New materials, including lightweight alloys and composites, are being developed, allowing for improved performance characteristics in the products produced via die casting. This trend promises to meet the growing demand for high-performance components in various industries.
4. Innovation in Mold Design
Continuous research leads to innovative mold designs that further enhance the efficiency and quality of die casting processes. Improved cooling systems and precision engineering are at the forefront of this trend.
Conclusion
The role of die cast mold manufacturers in the landscape of metal fabrication is substantial and multifaceted. As industries continue to demand higher efficiency, better quality, and improved designs, the importance of skilled manufacturers become increasingly vital. Companies like DeepMould.net exemplify the commitment to excellence in this field, providing unmatched service and products tailored to meet the evolving needs of various sectors.
Investing in the relationship with a proficient die cast mold manufacturer can lead to innovative solutions, cost savings, and enhanced product offerings, ultimately leading to a competitive edge in the market.
Understanding the nuances of die casting and the essential role that die cast mold manufacturers play can empower businesses and stakeholders to make informed decisions that positively impact production processes and product quality.