Injection Molding in China: A Comprehensive Guide to Metal Fabrication
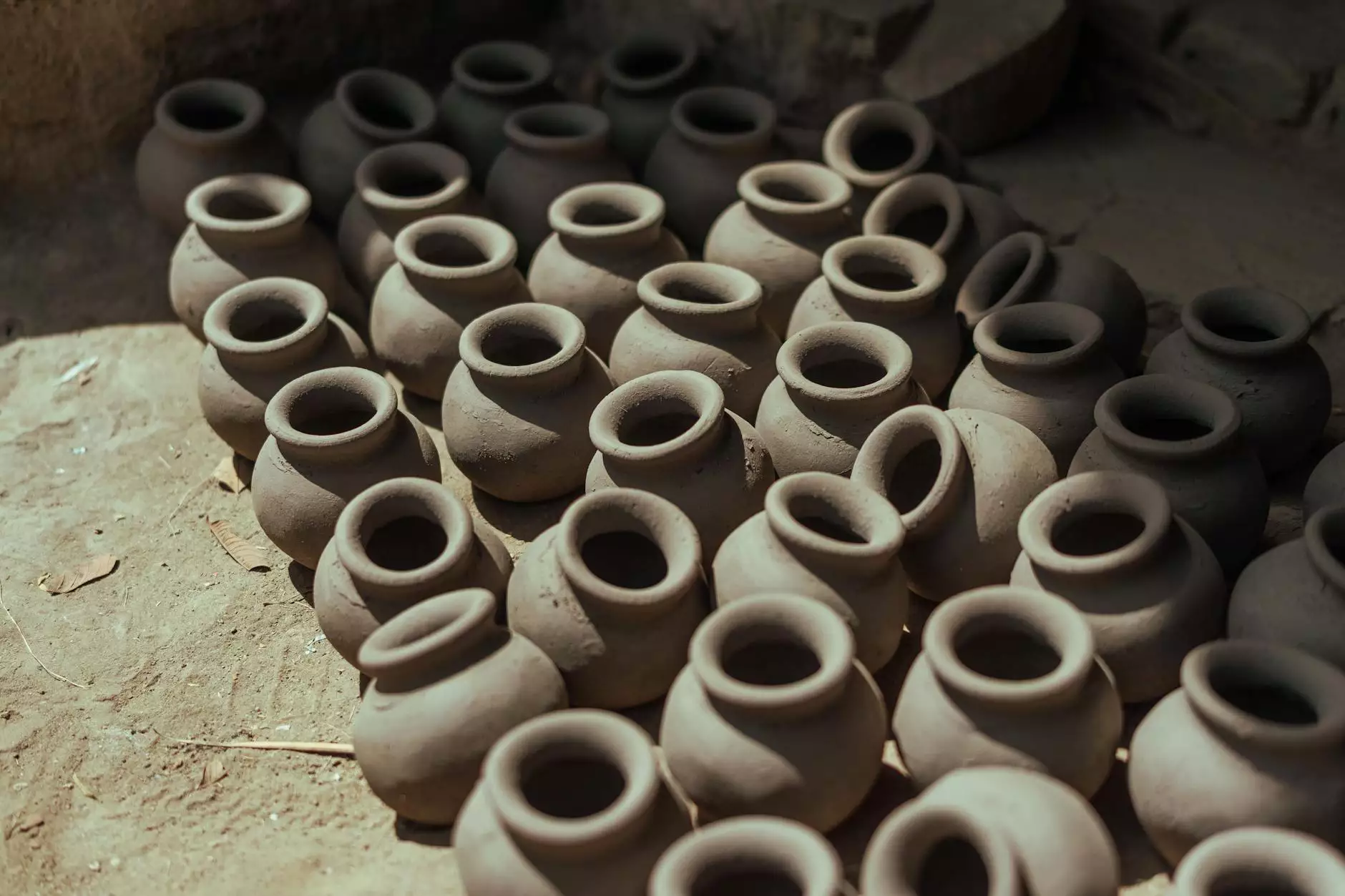
Injection molding in China has emerged as one of the leading manufacturing processes in the global economy. With its ability to produce intricate parts at scale and low cost, it is no wonder that manufacturers worldwide are turning to China for their Metal Fabrication needs. This article delves into the benefits, processes, quality standards, and future trends of injection molding in China, providing manufacturers and businesses with the information they need to make informed decisions.
The Rise of Injection Molding in China
China’s economic landscape has undergone a significant transformation over the past few decades. One of the most notable changes is the country's emergence as a manufacturing powerhouse. Injection molding is at the forefront of this transformation, driven by several factors:
- Cost-Effectiveness: Lower labor costs and material expenses make China an attractive option for companies seeking to minimize production costs.
- Advanced Technology: The adoption of cutting-edge technology and machinery enhances the precision and efficiency of the injection molding process.
- Skilled Workforce: A growing pool of skilled professionals in engineering and manufacturing ensures high-quality output.
- Government Support: Policies promoting manufacturing and foreign investment bolster the growth of the injection molding sector.
Understanding the Injection Molding Process
Injection molding is a highly sophisticated manufacturing process that involves the production of parts by injecting molten material into a mold. Here’s how it works:
Step 1: Material Selection
Various materials can be utilized in injection molding, including thermoplastics, thermosetting polymers, and metals. The choice of material is critical as it affects the final product's durability, function, and cost.
Step 2: Designing the Mold
The mold is a vital component of the injection molding process. It must be meticulously designed to ensure the final product matches the desired specifications. Advanced CAD software is typically used for this purpose.
Step 3: Heating the Material
The chosen material is heated until it reaches a molten state. This heating process is crucial, as it determines the flow characteristics of the material during injection.
Step 4: Injection Process
The molten material is injected into the mold at high pressure. This pressure ensures that the material fills every cavity in the mold, creating a precise replica of the intended design.
Step 5: Cooling and Ejection
Once the mold is filled, the material is allowed to cool and solidify. After sufficient cooling, the mold opens, and the finished part is ejected. This step requires careful timing to prevent damage to the product.
Advantages of Injection Molding in China
Choosing to utilize injection molding in China for metal fabrication presents numerous advantages:
- High Production Speed: Injection molding allows for rapid production of large volumes of parts, making it ideal for high-demand industries.
- Consistency and Quality: The automated nature of the process ensures high consistency and minimal variation in quality.
- Complex Part Design: Intricate designs and complicated geometries can be easily achieved through injection molding.
- Material Versatility: A wide range of materials can be processed, providing flexibility for different applications.
- Reduced Waste: The process produces minimal waste since excess material can often be recycled within the system.
Quality Standards in Injection Molding
Quality assurance is paramount in injection molding to ensure that products meet global standards. Manufacturers like DeepMould adhere to strict quality control measures, including:
- ISO Certification: Certification ensures that processes meet international standards for quality and efficiency.
- Material Testing: All materials undergo rigorous testing to confirm their durability and suitability for intended applications.
- Design Reviews: Regular design reviews are conducted to ensure alignment with production capabilities and customer requirements.
- End-of-Line Inspections: Final products are inspected to catch any defects before shipping.
Industry Applications of Injection Molding
The applications of injection molding span a multitude of industries. Some prominent sectors include:
1. Automotive Industry
Injection molding is widely used to produce various automotive components, ranging from dashboards to engine parts, thanks to its ability to handle complex designs and material specifics.
2. Consumer Electronics
In the realm of consumer electronics, injection molding creates enclosures, components, and intricate designs for gadgets and devices that demand precision and aesthetic appeal.
3. Medical Devices
The medical industry benefits significantly from injection molding, producing products such as syringes, surgical instruments, and diagnostic equipment that require stringent quality and safety standards.
4. Packaging
Injection molding plays a crucial role in producing packaging solutions that are both functional and visually appealing, including containers, caps, and closures.
The Future of Injection Molding in China
As the global economy evolves, the future of injection molding in China appears bright. Key trends shaping the industry include:
- Innovation in Materials: The development of new materials will expand the capabilities and applications of injection molding.
- Sustainability Efforts: Increased focus on eco-friendly practices, including the use of recycled materials and energy-efficient processes, will be essential for future success.
- Smart Manufacturing: The integration of IoT and AI technologies will enhance production efficiency, maintenance scheduling, and quality assurance processes.
- Customization: An increasing demand for customized products will lead to innovations in the design and manufacturing processes.
Choosing the Right Injection Molding Partner in China
Selecting the right partner for your injection molding needs is critical for achieving success. Here are some tips to consider when evaluating potential manufacturers:
- Experience: Look for companies with a proven track record in injection molding and a strong understanding of your industry.
- Technological Capabilities: Ensure the manufacturer has access to advanced machinery and technologies to meet the specifications of your projects.
- Quality Assurance Processes: Inquire about their quality control measures to confirm they align with international standards.
- Customer Support: Opt for manufacturers that provide excellent communication and support throughout the production process.
Conclusion
In conclusion, injection molding in China represents a core pillar of modern metal fabrication, offering companies unparalleled advantages in speed, cost, and quality. As you consider your options for manufacturing, embracing the capabilities provided by skilled Chinese manufacturers, such as DeepMould, can pave the way for innovative, timely, and cost-effective product development.
With ongoing advancements in technology, materials, and processes, the future of injection molding holds significant promise, making it an essential consideration for businesses that prioritize efficiency and quality in their production processes.
injection molding china