Understanding Precision Injection Molding: A Path to Excellence in Manufacturing
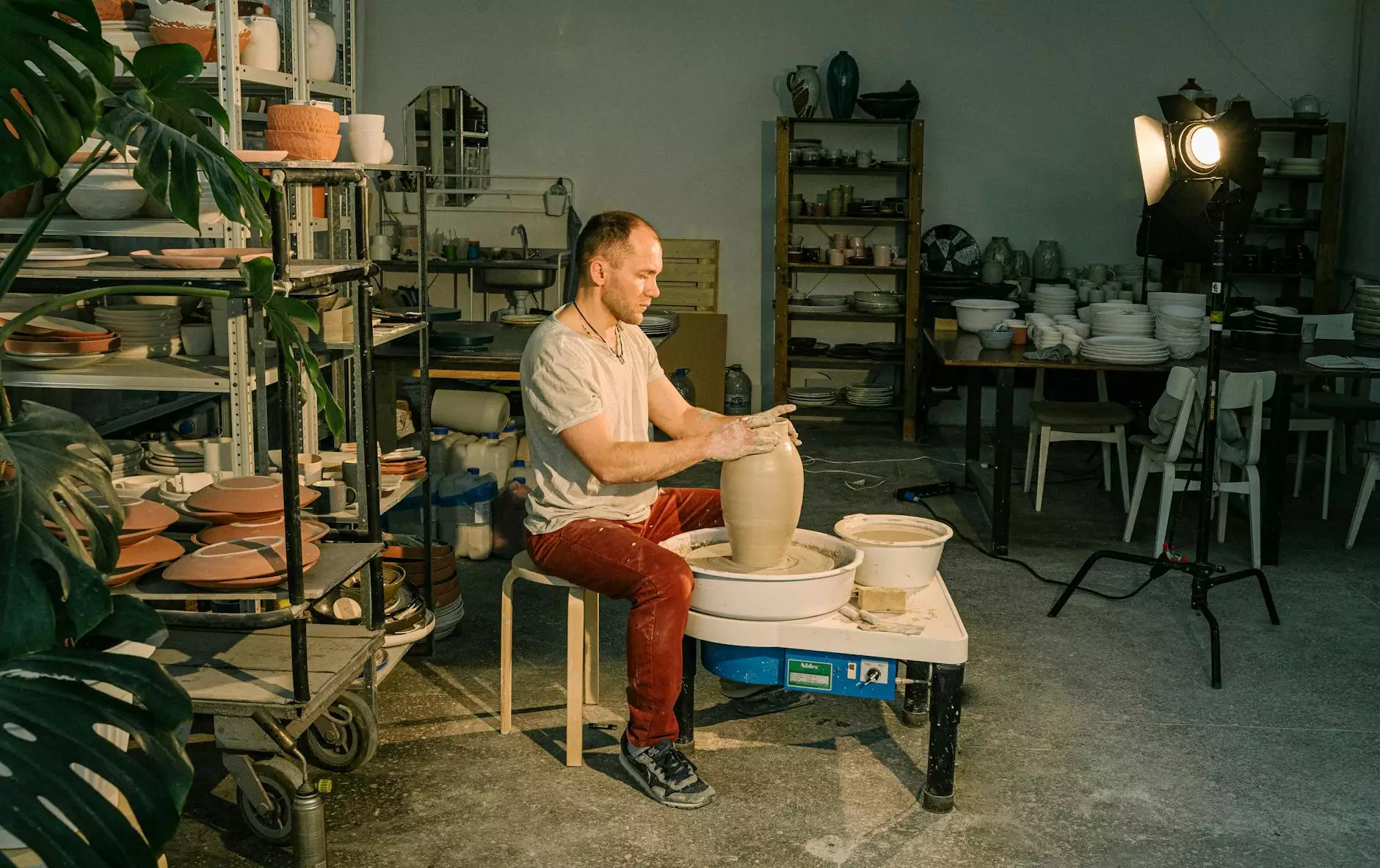
In the modern manufacturing landscape, precision is not just a goal; it is a necessity. Among the various methods employed, precision injection molding has emerged as one of the most efficient and effective techniques for producing high-quality plastic parts. As a leading precision injection molding manufacturer, Deep Mould embodies the principles of quality, precision, and efficiency, setting benchmarks in the industry.
What is Precision Injection Molding?
Precision injection molding is a manufacturing process used for producing items by injecting molten material into a mold. The molds are designed with high accuracy to ensure that every part meets the required specifications. The process begins with the melting of raw plastic or metal materials, followed by their injection into the mold where they are cooled and solidified to form the final product.
The Importance of Precision in Injection Molding
Precision in injection molding is crucial for several reasons:
- Quality Control: Ensures that each product meets strict tolerances and standards.
- Cost Efficiency: Reduces waste and the need for rework, thus lowering overall production costs.
- Speed: Allows for quick production cycles, making it ideal for high-volume manufacturing.
- Versatility: Used in a variety of industries, from automotive to medical devices, showcasing its adaptability.
How Precision Injection Molding Works
The process of precision injection molding involves several key steps:
1. Material Selection
The choice of material is critical in precision injection molding. Common materials include thermoplastics, thermosetting plastics, and metals. Each material has unique properties that influence the final product's performance and application.
2. Mold Design
Designing the mold is one of the most significant aspects of the process. A well-designed mold enables high precision and reduces the chances of defects during the injection process.
3. Injection Process
In this step, the selected material is melted and injected into the mold under high pressure. This stage requires careful control of temperature and pressure to ensure uniform distribution in the mold cavity.
4. Cooling and Ejection
Once the material is injected, it is allowed to cool and solidify. The cooling time is crucial as it affects the dimensional stability of the part. After cooling, the mold is opened, and the finished part is ejected.
Applications of Precision Injection Molding
Precision injection molding serves numerous industries and applications, showcasing its versatility:
1. Automotive Industry
In the automotive sector, precision-molded parts are integral to the production of components such as dashboard elements, housings, and connectors. The ability to produce durable and lightweight parts enhances efficiency and performance.
2. Medical Devices
The medical industry demands unmatched accuracy and hygiene standards. Precision injection molding is employed in manufacturing syringes, surgical tools, and other critical components, ensuring safety and compliance with regulations.
3. Consumer Goods
From household items to electronic devices, precision molding provides the consumer goods market with reliable and visually appealing products. It allows manufacturers to design complex shapes while maintaining quality.
4. Aerospace Components
In aerospace, the weight of components can drastically affect performance. Precision injection molding facilitates the creation of lightweight yet robust parts essential for aerodynamics and fuel efficiency.
Advantages of Working with a Precision Injection Molding Manufacturer
Choosing the right precision injection molding manufacturer can significantly impact your project's success. Here are some advantages:
- Expertise: Experienced manufacturers possess deep knowledge of materials and processes, ensuring optimal product performance.
- Technological Advancement: High-end manufacturers leverage the latest technology to enhance production efficiency and quality.
- Custom Solutions: Tailored designs and solutions to meet specific client requirements build strong partnerships and foster innovation.
- Scalability: The ability to meet large-scale production needs without compromising quality is essential for growing businesses.
Why Choose Deep Mould as Your Precision Injection Molding Partner?
At Deep Mould, we pride ourselves on being a leader in the precision injection molding space. Our commitment to quality, combined with an efficient manufacturing process, allows us to deliver exceptional outcomes. Here’s why partners choose us:
1. Quality Assurance
Our rigorous quality control processes ensure that every component produced meets the highest standards. We conduct thorough inspections to guarantee precision at every step, from material selection to finished product testing.
2. Advanced Technology
Utilizing cutting-edge machinery and software, we optimize the injection molding process for speed and accuracy. Our investments in technology translate directly into superior products for our clients.
3. Experienced Team
Our team of engineers and technicians possess immense expertise in precision injection molding. Their know-how drives our innovation and strengthens our manufacturing capabilities.
4. Commitment to Sustainability
We recognize the importance of sustainable practices and are committed to minimizing waste and reducing energy consumption throughout our processes. This not only benefits the environment but also provides cost savings for our clients.
Challenges in Precision Injection Molding and How to Overcome Them
While precision injection molding is a highly efficient process, it comes with its set of challenges. Here are some common issues and ways to resolve them:
1. Material Variability
Variability in material properties can lead to inconsistencies in the final product. It is crucial to source high-quality materials and collaborate closely with suppliers to ensure that raw materials consistently meet specifications.
2. Mold Wear and Tear
Molds can wear out over time. Regular maintenance and timely replacement of worn molds are essential to maintain production quality. Investing in high-quality molds can also minimize the frequency of replacements.
3. Process Optimization
Fine-tuning the injection molding process can be complex. Utilizing software for simulation and real-time monitoring can help optimize parameters, ensuring consistent results.
4. Cost Management
As production scales, costs can escalate. A detailed cost analysis and adopting lean manufacturing principles can help maintain profitability without compromising quality.
The Future of Precision Injection Molding
As industries evolve, the future of precision injection molding looks promising. With advancements in machine learning, automation, and sustainable practices, manufacturers will be able to produce even more complex shapes with enhanced performance characteristics. The integration of smart manufacturing techniques will further streamline processes, reduce costs, and improve product quality.
Conclusion
In summary, precision injection molding is a critical process in modern manufacturing with a myriad of applications across different industries. As a respected precision injection molding manufacturer, Deep Mould continues to lead the way by delivering high-quality, precision-engineered components that meet our clients’ stringent requirements. With a commitment to excellence, innovation, and sustainability, we are poised to remain at the forefront of the injection molding industry, helping businesses succeed.
For more information about how we can assist you in achieving your manufacturing goals, visit Deep Mould today!