Deep Flex Plastic Molds: The Future of Precision Manufacturing
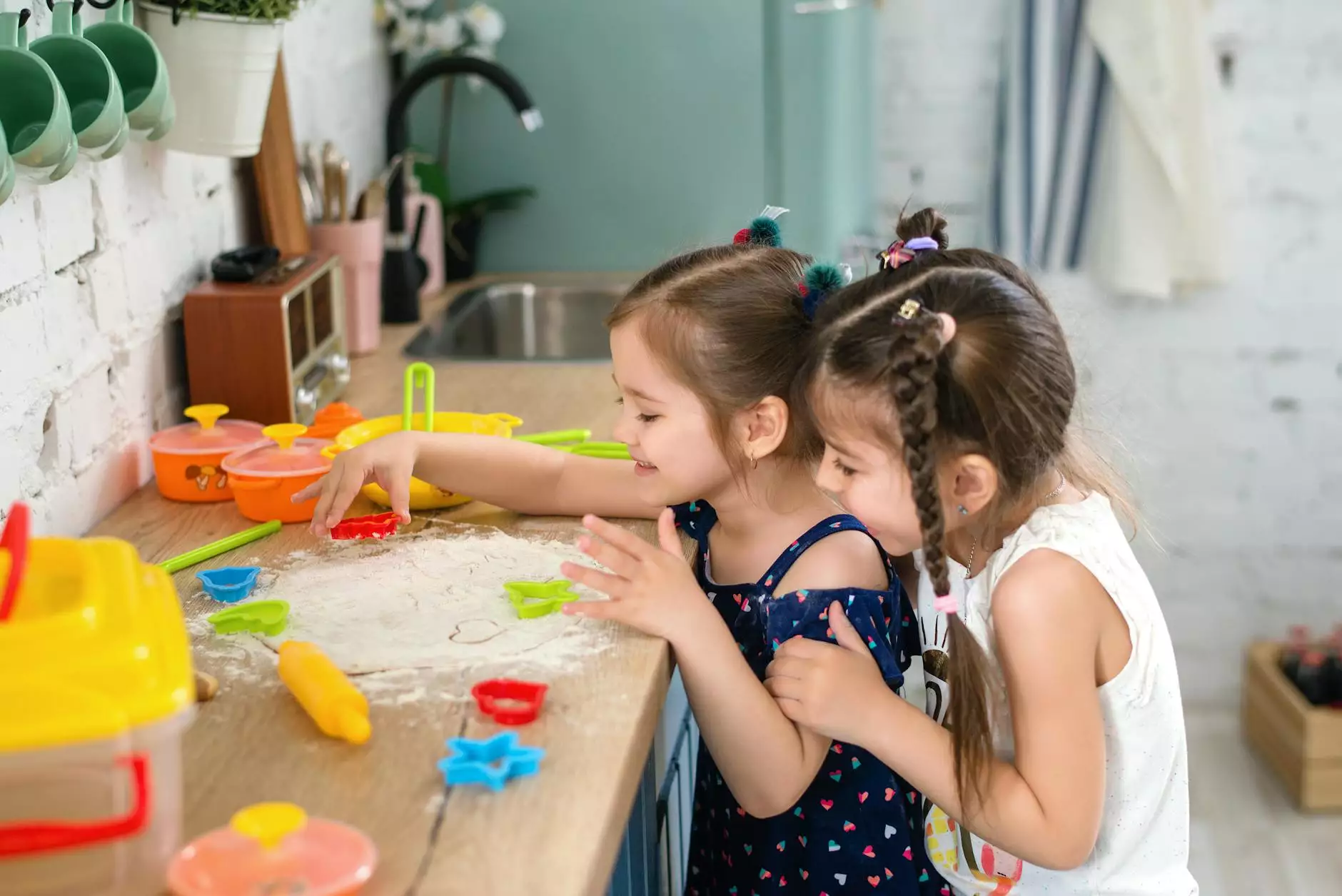
In the ever-evolving world of manufacturing, deep flex plastic molds have emerged as a pivotal innovation, providing unprecedented flexibility and efficiency in production processes. This comprehensive article delves into the intricacies of these molds, examining their significance, applications, and advantages for metal fabricators and other industries.
Understanding Deep Flex Plastic Molds
Deep flex plastic molds are specialized molds designed to create parts and components with complex geometries and intricate details. They are primarily utilized in the manufacturing sector, where precision and versatility are paramount. These molds are typically made using advanced materials that allow for flexibility and durability, making them suitable for various production methods, including injection molding and compression molding.
The Composition of Deep Flex Plastic Molds
The key to the effectiveness of deep flex plastic molds lies in their composition. Often made from high-quality thermoplastics or elastomers, these molds offer remarkable features:
- Durability: Able to withstand high temperatures and pressures, ensuring longevity.
- Flexibility: Their inherent flexibility allows for easy removal of molded parts, reducing risk of damage.
- Precision: Engineered to produce parts with tight tolerances and intricate designs.
The Role of Deep Flex Plastic Molds in Metal Fabrication
Metal fabricators play an essential role in various industries, including automotive, aerospace, and consumer goods. The integration of deep flex plastic molds into metal fabrication processes can enhance productivity and product quality. Here are several ways these molds can be beneficial:
1. Enhanced Design Flexibility
The ability to create complex designs without the traditional constraints of rigid molds makes deep flex plastic molds invaluable. Metal fabricators can:
- Rapidly prototype new designs, allowing for quicker iterations based on market feedback.
- Incorporate intricate features such as undercuts and internal geometries without sacrificing mold stability.
2. Cost-Effectiveness
Producing parts with deep flex plastic molds can significantly reduce production costs:
- The molds require less upfront investment compared to traditional metal molds, making them accessible for smaller businesses.
- Reduced cycle times contribute to efficiency, allowing fabricators to produce more parts within shorter timeframes.
3. Reduced Waste and Environmental Impact
Using these molds can lead to a decrease in material waste during production:
- Precision manufacturing: minimizes excess material use, contributing to sustainability.
- The ability to recycle and reuse materials is enhanced by the mold's design, benefiting the environment.
Applications of Deep Flex Plastic Molds
The versatility of deep flex plastic molds allows them to be employed across various industries. Here are some notable applications:
1. Automotive Industry
The automotive sector relies on precision parts for performance and efficiency. Deep flex plastic molds enable the production of components such as:
- Interior panels with complex shapes.
- Engine covers that require precise fitment.
2. Aerospace Manufacturing
In aerospace, where safety and performance are critical, the need for high-precision components is paramount. Deep flex plastic molds assist in producing:
- Lightweight structural components.
- Fuel system parts that must meet stringent regulations.
3. Consumer Goods Production
From household items to electronic casing, deep flex plastic molds are integral in manufacturing:
- Durable and affordable kitchen tools.
- Intricate electronic enclosures that require precise mold-fitting.
Technical Advantages of Deep Flex Plastic Molds
Beyond cost and flexibility, the technical advantages of deep flex plastic molds are noteworthy:
1. High Tolerance Levels
These molds provide a level of precision that is essential for high-performance industries. The ability to maintain tight tolerances leads to:
- Elimination of costly reworks.
- Improved product reliability and consistency.
2. Quick Turnaround Times
In today’s fast-paced market, speed is crucial. Deep flex molds reduce:
- Time from design to finished product.
- Set-up times in production lines, allowing for rapid response to trends.
3. Customization Potential
Manufacturers can tailor molds to meet specific customer needs, enhancing customer satisfaction through:
- Personalized products that stand out in a competitive market.
- Adaptation to changing market demands without significant retooling costs.
Conclusion: Embracing Deep Flex Plastic Molds for Future Success
The emergence of deep flex plastic molds marks a significant milestone in the evolution of manufacturing, particularly for metal fabricators. With their unparalleled flexibility, cost-effectiveness, and precision capabilities, these molds redefine efficiency and innovation.
As industries continue to embrace technological advancements, the integration of deep flex plastic molds will undoubtedly pave the way for new possibilities and enhanced manufacturing processes. It’s time for metal fabricators to leverage this technology to stay ahead in a competitive landscape, ensuring the delivery of quality products that meet the evolving needs of consumers and industries alike.
Call to Action
For metal fabricators looking to upgrade their production capabilities, exploring the world of deep flex plastic molds could be the key to unlocking greater efficiencies and innovative designs. Visit DeepMould.net today to learn more about our offerings and how we can assist you in achieving your manufacturing goals.