Plastic Injection Mold Manufacturers: Revolutionizing Metal Fabrication
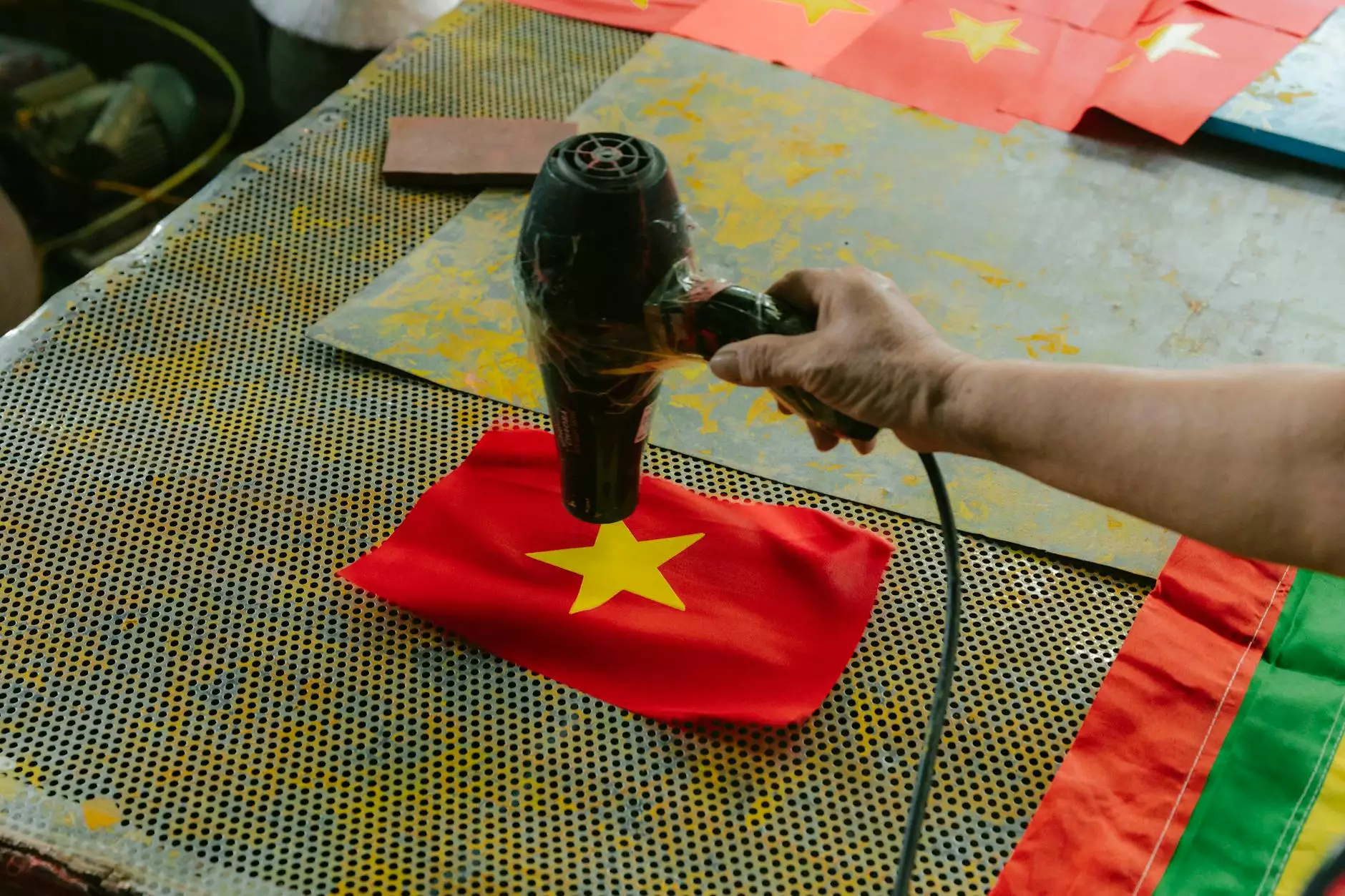
The world of manufacturing has evolved dramatically over the past few decades, and at the forefront of this revolution are plastic injection mold manufacturers. These companies play a crucial role in producing high-quality plastic products and components by utilizing advanced molding techniques. In this article, we will explore the intricacies of plastic injection molding, the benefits it offers, and how it integrates seamlessly with the metal fabrication industry.
Understanding Plastic Injection Molding
Plastic injection molding is a manufacturing process used for producing parts by injecting molten material into a mold. This method allows for the creation of complex shapes and high-precision components that are essential in many industries, including automotive, consumer goods, and electronics.
How Does Plastic Injection Molding Work?
The process of plastic injection molding involves several key steps:
- Designing the Mold: The initial step is to create a mold design based on the specifications of the product. This requires skilled engineers who can design for efficiency and precision.
- Creating the Mold: Once the design is approved, the mold is fabricated using materials such as steel or aluminum. The choice of material often depends on the production volume needed.
- Melting the Plastic: Plastic resin pellets are heated until they melt into a liquid form. This melted plastic is then ready to be injected into the mold.
- Injection: The molten plastic is injected into the mold at high pressure. This ensures that the plastic fills every cavity of the mold effectively.
- Cooling: The plastic is allowed to cool and solidify. This stage is critical for ensuring that the final product achieves the desired dimensions and properties.
- Extraction: Finally, the mold is opened, and the newly formed plastic part is ejected, ready for further processes such as finishing or assembly.
The Role of Plastic Injection Mold Manufacturers in Metal Fabrication
While plastic injection molding primarily focuses on plastic products, its impact on metal fabrication cannot be understated. Many metal fabricators rely on plastic injection mold manufacturers for producing key components that are used in conjunction with metal parts.
Integrating Plastic and Metal Components
In modern manufacturing, it is common to find products that combine both plastic and metal elements. This integration can enhance functionality, reduce weight, and lower production costs. For example:
- Automotive Industry: Plastic parts such as dashboards and interior components are often combined with metal frames and supports for strength and durability.
- Consumer Electronics: Many electronic devices feature plastic casings that protect sensitive metal components while providing a sleek appearance.
- Medical Devices: The combination of plastic and metal is vital in creating devices that are both lightweight and sterilisable.
Benefits of Partnering with Plastic Injection Mold Manufacturers
There are numerous advantages to working with plastic injection mold manufacturers in the metal fabrication process. Some of these benefits include:
1. Cost Efficiency
Plastic injection molding is often more cost-effective than traditional machining methods for high-volume parts. Manufacturers can produce numerous components quickly, reducing labor and material costs.
2. High Precision and Quality
With the advancements in technology, plastic injection molding allows for a very high degree of precision. This means that parts can be produced with incredibly tight tolerances, ensuring that they fit perfectly with their metal counterparts.
3. Design Flexibility
The design freedom offered by plastic injection molding enables manufacturers to create intricate shapes that would be difficult or impossible to achieve with metal fabrication alone. This flexibility encourages innovation in product design.
4. Reduced Lead Times
Plastic injection mold manufacturers typically maintain a fast turnaround time. Once a mold is created, parts can be produced at a rapid pace, allowing companies to meet market demands swiftly and efficiently.
Choosing the Right Plastic Injection Mold Manufacturer
When selecting a plastic injection mold manufacturer, several factors should be considered to ensure the best results for your project. Here are some key aspects to evaluate:
1. Experience and Expertise
Look for manufacturers with a proven track record in both plastic injection molding and collaboration with metal fabricators. Their experience can significantly influence the quality and precision of the final product.
2. Technological Capabilities
Assess the technology and machinery available at the manufacturer. Modern injection molding machines with advanced capabilities can enhance production efficiency and product quality.
3. Quality Assurance Processes
Ensure that the manufacturer has robust quality assurance measures in place. Certifications such as ISO can provide confidence in their manufacturing processes and product quality.
4. Flexibility in Production
The ability to adapt to production changes, whether in volume or design modifications, is crucial. A responsive manufacturer can better cater to your evolving project needs.
Future Trends in Plastic Injection Molding and Metal Fabrication
The landscape of manufacturing is constantly changing, and both plastic injection molding and metal fabrication are set to evolve. Here are some trends to watch:
1. Sustainable Manufacturing Practices
As awareness of environmental issues grows, both industries are moving towards more sustainable practices. This includes using recyclable materials and implementing energy-efficient manufacturing processes.
2. Advances in Materials Science
New materials are being developed that enhance the properties of plastics, making them more durable and suitable for a broader range of applications. These advances will likely transform the integration of plastic and metal components.
3. Automation and Smart Manufacturing
Automation is becoming a significant part of manufacturing, including in plastic injection molding. Smart factories that utilize IoT (Internet of Things) technologies can optimize production and improve efficiency.
4. Customization and Personalization
With the rise of consumer demand for personalized products, manufacturers must embrace customization. Plastic injection mold manufacturers are poised to offer tailored solutions that meet specific client needs.
Conclusion
In the competitive landscape of modern manufacturing, plastic injection mold manufacturers offer invaluable services that significantly enhance the efficiency and quality of production. Their ability to integrate with metal fabricators showcases the versatility and importance of their role in various industries. By understanding the benefits and processes of plastic injection molding, businesses can make informed decisions that propel them into the future of manufacturing.
For more information about how industry-leading capabilities in plastic injection molding can benefit your business, visit deepmould.net today!