Understanding Plastic Injection Molding
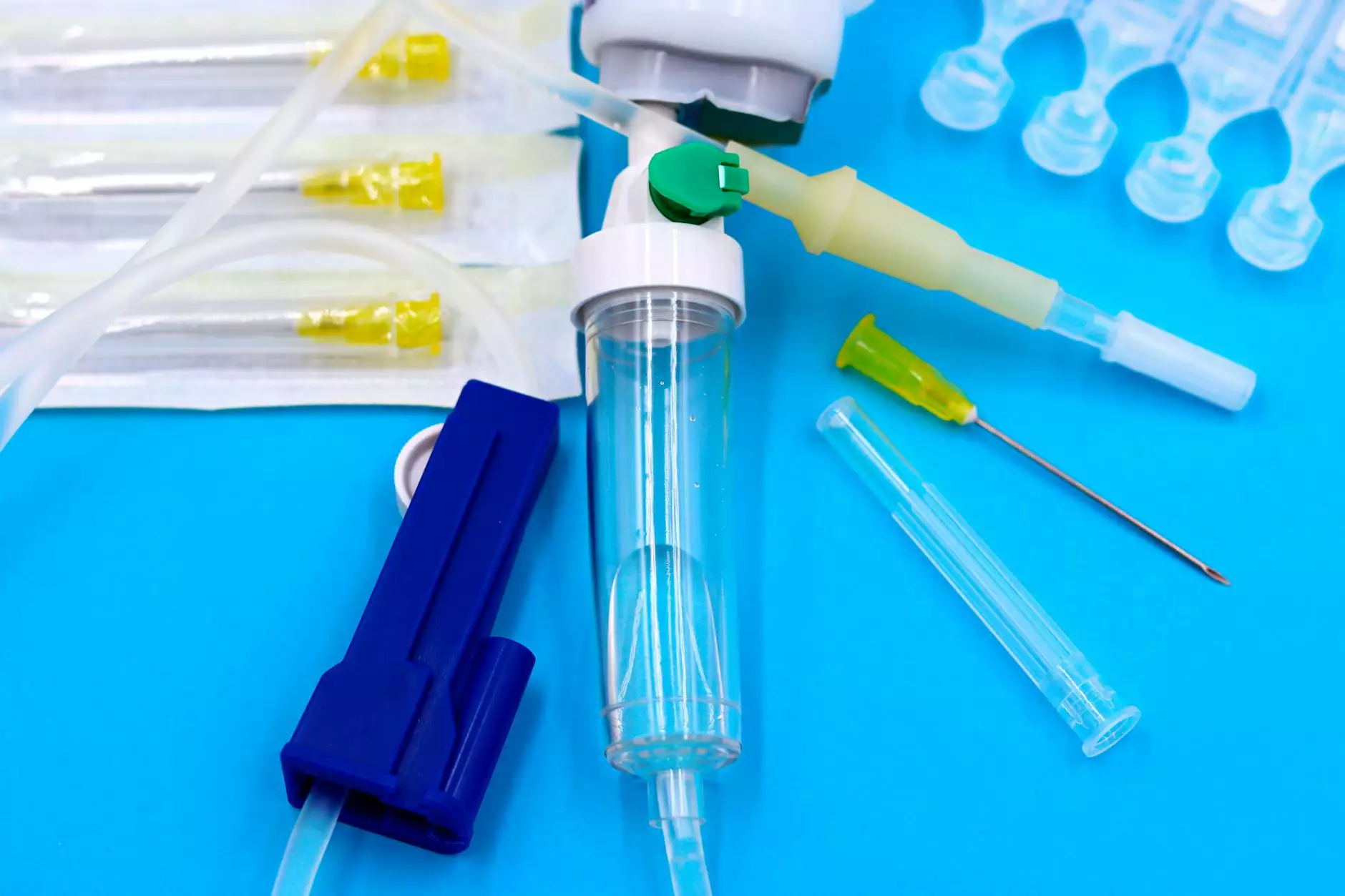
Plastic injection molding is a revolutionary manufacturing process that allows for the creation of complex parts with high precision and efficiency. This method has transformed various industries by enhancing the production capabilities and enabling the creation of intricate designs that were previously impossible to achieve. In this article, we will explore the details of plastic injection molding, its benefits, applications, and how it collaborates with other manufacturing processes.
What is Plastic Injection Molding?
Plastic injection molding is a process where molten plastic is injected into a mold to create specific shapes. The process begins with heating the thermoplastic material until it becomes pliable. The molten plastic is then injected under high pressure into a mold cavity. Once it cools and solidifies, the newly formed part is ejected from the mold. This method is highly efficient for mass production, allowing manufacturers to create thousands of identical parts quickly.
The Process of Plastic Injection Molding
The plastic injection molding process can be broken down into several key stages:
- Material Selection: Choosing the right type of plastic based on the desired properties of the final product.
- Melting: The plastic is heated in a barrel until it reaches a molten state.
- Injection: The molten plastic is injected into the mold at high pressure.
- Cooling: The plastic cools and solidifies into the desired shape.
- Ejection: The finished part is ejected from the mold.
- Finishing: Additional processes may be applied, including trimming, painting, or assembly.
Advantages of Plastic Injection Molding
There are numerous advantages to using plastic injection molding in manufacturing, including:
- High Production Efficiency: Capable of producing a large number of parts within a short time frame.
- Cost-Effectiveness: Economical for mass production due to reduced labor and material costs.
- Design Flexibility: Supports complex designs that can be difficult to achieve with other manufacturing processes.
- Consistency: Ensures high levels of precision and uniformity across all molded parts.
- Reduced Waste: Minimal material waste compared to traditional manufacturing methods.
Applications of Plastic Injection Molding
Plastic injection molding is utilized across various industries, demonstrating its versatility. Some common applications include:
- Automotive Industry: Manufacturing components such as dashboards, clips, and housings.
- Consumer Goods: Creating items like kitchen utensils, toys, and electronic housings.
- Medical Devices: Producing critical components such as syringes, inhalers, and diagnostic devices.
- Aerospace: Making lightweight components that meet stringent safety and performance standards.
- Packaging: Creating containers and packaging solutions that are both functional and visually appealing.
The Role of Sumiparts in Plastic Injection Molding
At Sumiparts.us, we specialize in providing high-quality manufacturing services, including plastic injection molding. Our expertise encompasses various aspects of production, ensuring we meet the specific needs of our clients. We boast a range of capabilities spanning across machining, laser cutting, welding, and vulcanization.
Integration with Other Manufacturing Processes
Plastic injection molding can be effectively integrated with other manufacturing processes to enhance product offerings. Here’s how:
- Machining: Precision machining can be used after injection molding to achieve tighter tolerances or unique features that the molding process cannot deliver.
- Laser Cutting: Laser cutting can create intricate shapes or patterns on molded parts, adding value and aesthetic appeal.
- Welding: Welding can be used to assemble multiple molded parts or attach components to create a complete product.
- Vulcanization: This process is used for rubber and can be combined with injection molding for parts that require elastic properties.
Choosing the Right Plastic for Injection Molding
The selection of the proper plastic material is critical in the plastic injection molding process. Factors to consider include:
- Mechanical Properties: Strength, flexibility, and durability requirements.
- Thermal Stability: Temperature resistance and behavior during the molding process.
- Cost: Budget constraints and material availability.
- Aesthetic Qualities: The color, texture, and finish of the final product.
Challenges in Plastic Injection Molding
While plastic injection molding offers numerous benefits, it also presents some challenges:
- Mold Design Complexity: Designing a mold can be intricate and time-consuming, requiring substantial expertise.
- Initial Costs: High initial investment in mold creation and machinery.
- Material Limitations: Not all plastics are suitable for all applications, and some may have limitations regarding the molding process.
- Defects: If not properly managed, defects such as warping, surface imperfections, or incomplete filling can occur.
Future Trends in Plastic Injection Molding
The future of plastic injection molding is promising, with several trends shaping its evolution:
- Sustainability: Increased focus on using recycled materials and developing eco-friendly alternatives.
- Advanced Technologies: Adoption of automation and robotics to optimize production processes.
- Smart Manufacturing: Use of IoT and data analytics to monitor processes and improve efficiencies.
- Customization: Rising demand for customized solutions to meet unique customer requirements.
Conclusion
In conclusion, plastic injection molding is a vital manufacturing process that significantly contributes to modern production across various industries. Its combination of efficiency, design flexibility, and cost-effectiveness makes it a preferred choice for mass production. At Sumiparts.us, our commitment to excellence and innovation in manufacturing allows us to provide tailored solutions that meet the diverse needs of our clients. Whether you need machining, laser cutting, welding, or vulcanized products, we are here to offer our expertise in achieving your manufacturing goals. Explore the possibilities with plastic injection molding today and see how it can elevate your product offerings to new heights.